When the full production time of a part lasts multiple years, process improvement is as tantalizing as failure is disastrous. This hasn’t stopped BWX Technologies’ Euclid, Ohio, facility from finding ways to optimize its processes, as the shop has reduced setups through implementing WFL multitasking machines, avoided crashes through simulation software and consolidated inspection needs through in-process measurement.
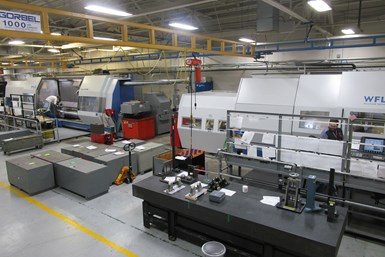
Each machine at BWXT uses an isolated, dedicated foundation to reach the close tolerances its parts require. All images courtesy of BWX Technologies.
Nuclear Requirements
BWXT focuses on manufacturing for the nuclear energy, defense and spaceflight markets. No one facility produces all the components for an application, as seen in a common job at the Euclid facility: producing electro-mechanical components for the US Navy’s aircraft carriers and submarines, which are then assembled into larger components at other facilities.
Featured Content
These parts must function for decades, and failure could be catastrophic. As such, the shop must ensure every part meets robust quality and technical requirements. At the same time, parts can be worth six-figures each; raw materials can take over a year to arrive at the facility; and the full production, fabrication, and testing process can extend over several years — making scrap a non-option.
The pressure is high, and the process itself adds yet more difficulty: the shop uses custom variants of stainless steel, hardened steel, carbon steel and Inconel. Tolerances average ±0.005 inch, but can reach extremes down to ±0.0001 inch.
These parts can range from the size of a water bottle to 10 feet long with a two-foot diameter. Parts can include 10 to 15 different welding operations, and assemblies can include 70 components. Lot sizes are small — typically between 10 and 50 pieces — so the shop does not rely on automation to streamline production.
To tackle these difficulties, the shop uses an array of CNC lathes, mills and grinders, as well as a handful of manual and secondary machines. BWXT has also increasingly adopted WFL mill-turn machines over the past decade, a change that has improved the shop’s process across multiple departments.
Simpler Setups
BWXT installed its first WFL machine, an M65 with a 4.5-meter bed length, in 2014. No one incident precipitated this change, but the shop had spent a long time reflecting on the decision beforehand. Its many individual lathe and mill operations risked misalignments with every setup, and as completing each setup required between one and three shifts, their large number was cause for frustration. Combining setups on a mill-turn machine was tempting, and the machines’ advertised accuracy and precision met BWXT’s needs.
In practice, the WFL machines combine turning work from BWXT’s two-axis lathes with some boring operations, as well as four-axis horizontal milling work. While this isn’t enough to complete parts in a single clamping, Zachary Sipos, a continuous improvement engineer for BWXT Euclid, says this has consolidated some routings requiring upwards of 10 operations by between three and five operations — resulting in a 200-300% productivity increase.
Sipos also says that horsepower and performance is comparable to or better than the mills and some of the lathes. This enables BWXT to combine proven manufacturing techniques with more efficient tooling and workholding for improved metal removal rates.
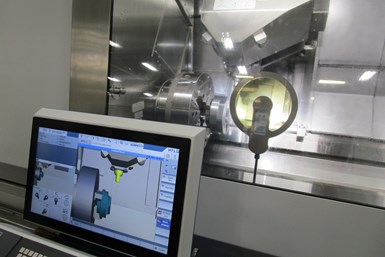
On-machine instances of WFL’s CrashGuard simulation software enable machinists to track operations as they happen — even in situations where high-pressure coolant would restrict visibility.
BWXT has since adopted several additional mill-turns to take advantage of this performance. Currently, it uses six M65s and a single M35. The bed length differs between these machines, making them suitable for different components, and some feature additional customizations.
Notably, one of the M65 machines has nine slots for prismatic tooling — the 250-pound and larger boring bars the shop sometimes uses — whereas most only have two. All the machines include 90 tool slots, which Sipos says enables redundant tooling and is a big upgrade from the eight to 12 tooling slots of most lathes.
Also an upgrade? The relative ease and simplicity of setting up parts in the WFL machines has enabled the shop to machine parts in smaller lots without affecting productivity or throughput. Grant Honroth, BWXT Euclid’s deputy general manager, says this saves months of production time. BWXT can also now produce ID and OD splines through hobbing cycles on its M35, a process that the shop could previously only perform on manual machines in its toolroom.
Real-Time Simulation
None of this would matter if the parts came out incorrectly, however, which is why BWXT puts a lot of stock in the CrashGuard software that it purchased for the WFL machines. CrashGuard is a WFL-proprietary simulation software that consists of two components: an offline version called CrashGuard Studio for programmers working at a computer, and an on-machine version that runs in real time.
WFL supplies models of each machine for CrashGuard Studio based on the machine’s serial number, enabling programmers to be sure of the programs they send to the shop floor.
On the shop floor, the software simulates fixturing, tooling and components in real time, so potential collisions with unexpected differences — for example, a steady rest — set off alarms well in advance of potential problems. BWXT’s operators can also use the real-time model to track production when they use high-pressure coolant, which can otherwise obscure the tool and the cut.
Preventing crashes is vital for the shop, as even with a nearby WFL support center in Wixom, Michigan, fixing the machine and redoing all the alignment and compensation work to BWXT’s standards (to say nothing of solving the problem that led to the crash in the first place) could require weeks or even months of downtime.
Tried and True Tech
This is true for the shop’s other machines, too, which use Vericut for programming-side simulation. BWXT utilizes about 45 CNC machines other than the WFLs, and uses between 20 and 30 manual machines and secondary machines for specific operations.
Manual machines may not be able to handle the tolerances BWXT requires, but the shop still gets good use from them for jobs like skim cuts and material testing. Secondary machines, meanwhile, take the form of jig mills, jig bore grinders and other specialist types of grinders that produce and finish certain types of tight tolerance holes. Honroth points to the example of one of the shop’s Mitsui Seiki jig grinders, which can produce holes at tolerances of 0.00005 inch.
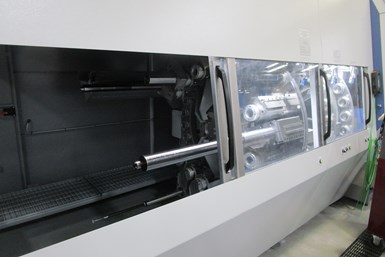
BWXT double-checks the mechanical accuracy of new machines with in-house laser compensation, and also performs yearly preventative maintenance to ensure high performance. But even that is not enough to prevent waviness on long parts — the shop uses compensation tables to make “taper edits” adjusting for tool wear as the tool machines across the part.
Proving the Tech
Inspection and measurement processes are currently similar between BWXT Euclid’s WFL machines and the rest of the shop’s machining fleet, but this could change in the future. The WFL machines can perform in-machine probing, but the shop is still proving out this technology.
Currently, BWXT primarily uses the in-machine probing to establish parts’ location and orientation, improving comparative measurements of machined features to established datum features. It then conducts final measurements using dedicated metrology equipment.
Because BWXT inspects every feature on every part, this takes a lot of time. Inspection personnel must be trained in snap gages, notch watches, dial bores, Zeiss CMMs and other gages that are six- or eight-feet long — and even then, the equipment can’t handle every part. For extremely long parts (or for setting long boring bars), the shop must touch off a known surface and use machine coordinates to measure dimensions.
BWXT is gradually proving out the in-machine probing on the WFL machines, testing its reproducibility and repeatability for as many measurements as possible. Some measurements, like surface finish, currently take place outside the machine due to the nature of the previous operation — in this case, the presence of coolant could ruin the indicators.
An important point of note is that many Industry 4.0 ideas are incompatible with BWXT’s needs. Strict security protocols stymie most web-based software, making other kinds of process improvement more valuable.
Demand for BWXT’s products has only increased since 2014, and the Euclid facility has even expanded 25% within the last four years to keep up with demand. Improvements to process efficiency are necessary to meet deadlines, even in a shop where those deadlines can be years away. Improvements to process efficiency that give users warnings about potential crashes or scrap are more valuable still.
Improvements that do both, while meeting increasingly stringent Department of Defense cybersecurity requirements? For BWXT: well worth the risk.
RELATED CONTENT
-
Improve Machining Efficiency Through Digital Twin Simulation
Full simulation of a machining cycle using digital twins can not only identify crashes before they happen, but provide insights that enable the user to reduce cycle times.
-
Simulation and Tooling Secure High-Value Work
Simulation software and careful attention to tooling parameters have enabled Major Tool to take on ambitious projects with its complex machinery.
-
Automation Solutions, Multitasking Machines Take Center Stage at Machine Fest 2023
Methods Machine Tools' Chicago-area Machine Fest saw over 15 live demos and more than 20 industry vendors over its two days, with a noticeable presence of automation solutions and multitasking machines.